Device reliability can be defined "Performing desired function in application for a certain period of time without mal-function" when the device used in application as component. To express reliability in a countable way, it can be the reliability level or defective rate and in a distribution functional way applying time as changeable exponent, exponent distribution or Weible distribution in semicon-ductor field. Figure 1 shows time parameter of defective rate between general electronic component and semiconductor, which has certain tendency.
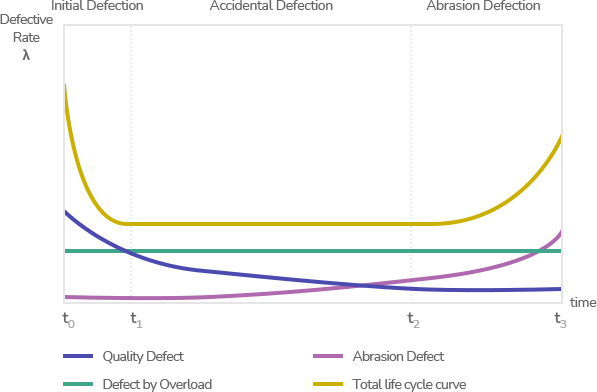
Failure period can be divided by three and each is Initial (Initial Failure Period)
Random (Random Failure Period), Wearout (Wearout Failure Period)
Semiconductor has tendency of gradual decrease during random failure period and it means accidentally random so to decrease such a failure is important. When express semiconductor reliability, several distributional functions can be used in approximate way, and reliability function R(t) can be expressed in following way in assumption of exponent distribution.
R(t) = exp(-λt)
The instantaneous failure ratio λ(t) and average life μ can be expressed following way.
λ(t) = λ(constant irrespective of time lapse)
μ = 1/λ = MTTF
In general semiconductor failure rate can be represented to %/1,000 hours by (t) = 1,000.
Since ailure is rare and the failure ratio is small judging from the field data and estmated failure ratio,
1/104 times this value [Namely 10-4(%/1,000hour) = 10-9(failures/hour)] is used under the nit of 1 Fit.
Regarding semiconductor eliability, it has to be taken onsideration that not only device itself but other functional stress and environmental strss can take effects.
These stresses have close relationship so here is explained about more important factor to use semiconductor reliably.
Environmental condition such as voltage and current is very important factor decides reliability of semicon-ductor.
Depending on the circuit adequate device selection and setting up right functional point have to be made.
Integrated circuit failure rate is highly affected by temperature and high temperature increases failure rate.
However small signal integrated circuit has small voltage and current so shouldn’t be concerned except specialized circuit.
If certain variation acceptable limit is confirmed and can give some room when designing surge voltage impress or focused on character variation, device life cycle and further application life cycle will prolong.
Electrical integrated circuit using relatively high voltage and current has higher current than voltage so elec- tricity consumption rate is so high.
Electricity consumption causes heat so it is not good in reliability matter.
To use integrated circuit reliably, it is good to use with decreased maximum voltage and current but decrease has meeting point with economical matter so it is hard to designate certain number.
In general following is standard.
Voltage70~80% or less for maximum rating
Power50% or less for maximum rating
Current80% or less for maximum rating
Temperature70~80% or less for maximum rating
In some cases government organization makes standard or design criteria to limit usage scope.
"The automatization of production processes and the improvement and progress of production technology have been outstanding.
The quality and reliability of devices have continued to be improved year after year thanks to such develop-ment, and by positively adopting newly developed technology.
It has probably been stated that there are no variations in quality thanks to the use of modern controlling methods and the full automation of processes.
However, devices are extremely small in shape, structure, and size, and are based on microtechnology for conducting their high-precision control, reinforced by physi-cal and chemical technology.
Therefore, even the slightest deviation exercises a large influence upon a device’s characteristics.
It is rather difficult to maintain various types of characteristics uniform, even by marking full use of today’s latest technology."
"The housings of semiconductor products are classified into the plastic resin-sealed type and the airtight-sealed type using metal. The plastic resin-sealed type, less expensive and possible to mass produce, recently has been employed in the majority of cases, covering application ranges from small signal to large power device.
This trend is backed by the facts that resins with high mechanical strength and excellent electrical insulation and resistance against environmental factors have been developed and employed, and that the reliability of this type has been greatly enhanced thanks to progress in molding techniques and surface treatment know-how.
The plastic resin-sealed type up to now has reached the level of the airtight-sealed type except concerning special environments, although devices are subjected to many environments in the markets.
Since the plastic resin-sealed type is not airtight, humidity in filtrates the device interior through the resin.
It is recommended employing the airtight-sealed type if the equipment or system is intended for use under a high humidity environment or when high reliability is required.Be careful not to directly expose semiconductor products to dust, harmful gases, salty (sea) air, radioactiverays, or similar environments; otherwise, they will suffer from unstable characteristics or rust in the lead wires."
JJESD22Semiconductor device test method
EIAJ ED-4701 Environmental and endurance test methods for semiconductor devices
EIAJ ED-4702 Mechanical stress test method for semiconductor surface mounting Devices
MIL-STD-202 Test method standard electronic and electrical component parts
MIL-STD-750 Test method standard semiconductor devices
MIL-STD-883 Test method standard Microcircuits
JIS C7021Environmental testing method and Endurance testing method for discrete semiconductor devices
JIS C7030Transistor test method
JIS C7032Transistor general regulation
JIS C7210General regulation of reliability assurance on each device
-
- 01
-
Product Strategy
-
- 02
-
Examining deelopment possibility
-
- 03
-
Development PP
-
- 04
-
Reliability evaluation
(non-regular)
-
- 05
-
Development complete
-
- 06
-
Manfacturing PP
-
- 07
-
Reliability evauation
(Lot Link)
-
- 08
-
Manufacturing Start
-
- 09
-
Reliability evaluation (regulation)
-
- 10
-
Product forward
-
Non-periodical reliability
Developing product, raw material/production process/Test to
prove facillty alteration in the aspect of reliability 1,008Hr -
Lot Link reliability
Test to check manufacturability of testimonial products
(168Hr test) -
Periodic reliability
Test to prove the quality assurance in the aspect of reliability.
(1,088Hr evaluation)